

CASE STUDY ONE
PORT OF FELIXSTOWE
​
The solid lubricant friction management systems have been operating on the ship to shore cranes at Felixstowe for over 10 years. Prior to their adoption, Felixstowe carried out extensive testing of the friction modifiers and demonstrated the benefits in terms of wheel and rail wear and improved tracking of the wheels on the rails, thus much reducing flange contact.

These benefits led to the system being retrofitted to virtually all the ship to shore cranes, which were from several OEM suppliers, and suitable brackets were designed and supplied for the different types.

All new cranes are now specified to use the friction modifier system and this helps maintain the reliability and availability of over 30 cranes operating at this critical economic hub for imports and exports from the UK.
​
Felixstowe is by far the largest container port in the UK and is continually improving its position by investment in new shipping berths and railway facilities and pursuing environmentally beneficial technology.

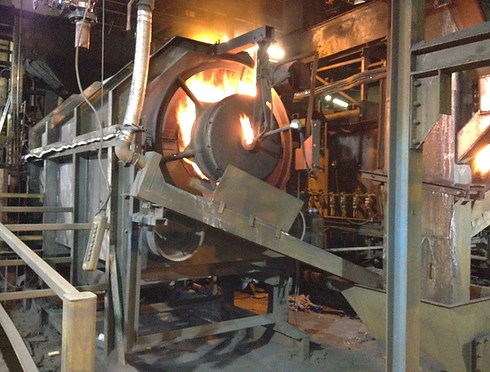
CASE STUDY TWO
ERVIN AMASTEEL
​
You won't find many more aggressive environments than at Ervin Amasteel at Tipton. Here they make shot and grit and some of this inevitably pervades the plant and creates many challenges including the severe wear of rolling components. On some of their rotating furnaces and driers, the track rings and trunnion rollers can wear away in 6 months requiring costly replacement to recover up to 40mm of wear.
In this environment, oil or grease is not a solution but a further liability, attracting even more abrasive material to the rolling surfaces. Ervin Amasteel, however, has identified GS solid lubricant (SL) sticks from BVY Industrials as the best technology to provide lubrication without the unwanted side effects of oil or grease. Previous tests with carbon based sticks had proved to be very disappointing, however, a trial with the GS lubricant sticks was set up and carefully monitored on one drier. The results were unequivocal; wear was reduced eight-fold and the usual 6 monthly replacement of worn components has been put back indefinitely. The pay-back on the equipment cost was less than 3 months.
​
CASE STUDY THREE
LAFARGE
​
One of the largest kilns now in the UK is operated by Lafarge UK Ltd, part of the multi-national Group. This impressive, KHD machine, 65m long and 4.2m diameter with its characteristic satellite coolers, forms a key part of the Lafarge cement production in the UK. Of the four support trunnions, the major load carrying one was showing distress with the roller bearings overheating regularly. The usual graphite lubrication block on the rollers was not helping here and Kelsan SL sticks were applied. These showed marked improvement and, coupled with other adjustments to the kiln alignment, have stabilised the trunnion and bearing temperatures ever since.

The pier 3 roller is a massive 1.06m wide and needed 16 SL sticks to cover this width. The use of individually applied sticks greatly improves the delivery efficiency of the product and allows the optimum lubrication to be supplied to the bands on the roller/tyre where the maximum contact pressures are exerted, whereas other bands receive a lesser dose. This self-regulating feature makes the system very cost-effective for such plant operators.
​


CASE STUDY FOUR
DEMATIC
​
The workhorse of many storage and retrieval systems used in high-bay warehouses across the country and worldwide is the AS/RS crane. Dematic is a world leader in supplying these along with many other key components of the logistics for component/materials management. These AS/RS cranes each run incessantly in an aisle on a single rail track to access the storage bins up to 30m high. The cranes with their payloads can be as heavy as 15 tonne supported on the rail by just 2 wheels.
The wheels and the rails of such systems frequently experience substantial wear and damage resulting from the heavy duty environment. Most operators were resigned to this and to the regular and costly wheel changes that were often an annual expense.
BVY Industrials was able to propose to Dematic an extremely efficient solution to this situation using a unique wheel tread friction modifier system, the SFM GS system. But Dematic quite rightly wanted to assess the technical and cost-effectiveness of the proposed system. They initiated a trial at one of their sites with careful and regular measurements on a test crane fitted with the SFM GS system compared with an identical control crane without the system fitted. Very quickly quite astonishing results were evident. But the trial was scheduled to continue to show conclusively that the results were consistent and valid. Finally the trial end results were available showing the remarkable reductions in wheel wear as can be seen from the wear charts and as reported by the Dematic Test Engineer who wrote:
“ I have attached the latest readings to show you the difference your sticks have made. Absolutely great results. The wheels on the control crane are now almost ready for a change and the test crane wheels are still like new. I am amazed that my manager has not yet ordered them for all the cranes.”
That order was not long in coming and Dematic has now rolled out installation to many of their sites including the mammoth Tesco Warehouse at Middlesbrough with 40 AS/RS cranes.
​